The Benefits of Laser Welding Equipment for Metal Fabricators
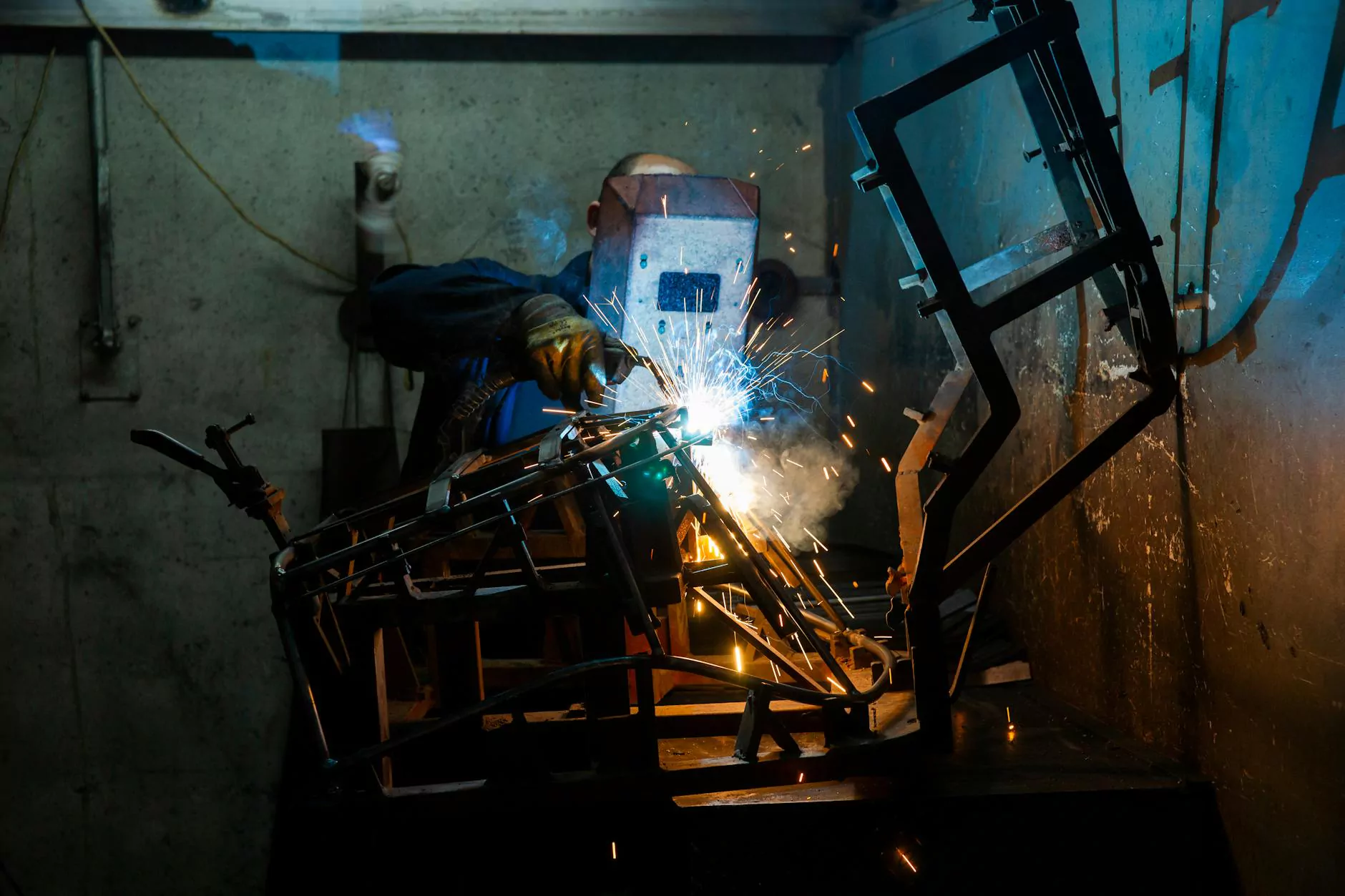
In today's competitive world of metal fabrication, laser welding equipment has emerged as a game-changer, offering precision, efficiency, and cost-effectiveness like never before. As a leading player in the industry, DP Laser provides cutting-edge solutions to meet the demands of modern metal fabricators.
Enhanced Precision and Accuracy
One of the key advantages of using laser welding equipment is the unparalleled precision it offers. The focused beam of laser light enables fabricators to achieve intricate welds with utmost accuracy, even on complex geometries. This level of precision results in higher quality finished products with minimal rework required.
Efficiency and Speed
Time is money in the world of metal fabrication, and laser welding equipment excels in delivering exceptional efficiency and speed. The high energy density of the laser beam allows for rapid heating and cooling of the material, leading to faster welding processes. This means that metal fabricators can increase their productivity and throughput without compromising on quality.
Cost-Effectiveness
Investing in laser welding equipment can yield long-term cost savings for metal fabricators. The precision of laser welding reduces material waste and minimizes the need for post-welding processes, saving both time and resources. Additionally, the speed of laser welding operations translates to lower labor costs and increased profitability for businesses.
Versatility and Adaptability
Metal fabricators are constantly faced with a wide range of materials and applications, and laser welding equipment offers unparalleled versatility and adaptability to meet diverse needs. Whether welding thin sheets of stainless steel or thick aluminum components, laser technology can be customized to deliver optimal results across a variety of materials and thicknesses.
Automation and Integration
With the advancement of laser welding equipment, automation has become increasingly prevalent in metal fabrication processes. DP Laser specializes in integrating laser welding systems with robotics and computer-aided design (CAD) software to streamline operations and enhance overall efficiency. By automating repetitive tasks, metal fabricators can improve consistency and precision while reducing human error.
Quality Control and Inspection
Ensuring the quality of welded components is paramount in the metal fabrication industry. Laser welding equipment enables real-time monitoring and inspection of welds, allowing for immediate adjustments to parameters if deviations are detected. This level of quality control guarantees that finished products meet the highest standards of durability and reliability.
Environmental Sustainability
As sustainability continues to gain importance in the manufacturing sector, laser welding equipment proves to be a greener alternative to traditional welding methods. The precise nature of laser welding reduces energy consumption and material waste, contributing to a more environmentally friendly production process. By embracing laser technology, metal fabricators can minimize their carbon footprint and uphold eco-friendly practices.
Conclusion
In conclusion, the adoption of laser welding equipment is a strategic move for metal fabricators looking to stay ahead in a competitive market. DP Laser, with its cutting-edge solutions and commitment to innovation, empowers businesses to achieve superior quality, efficiency, and cost-effectiveness in their welding operations. By investing in laser technology, metal fabricators can unlock a world of possibilities and elevate their success in the dynamic field of metal fabrication.