Plastic Rapid Prototypes Manufacturers: Revolutionizing Product Development
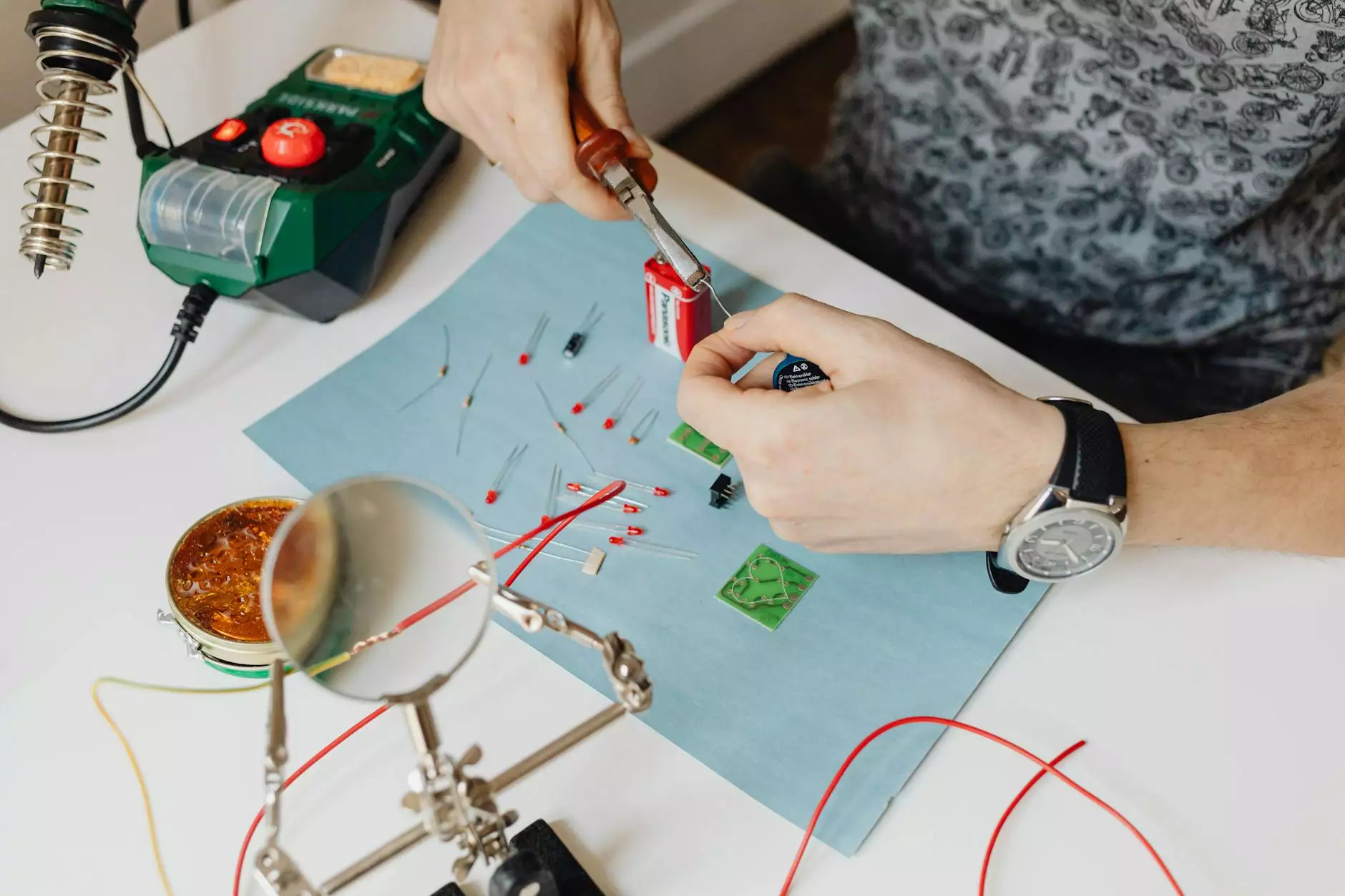
In today's fast-paced industrial landscape, plastic rapid prototypes manufacturers play a pivotal role in the product development process. These innovative companies help businesses transform their ideas into tangible prototypes, bridging the gap between concept and reality. By utilizing advanced technologies and methodologies, plastic rapid prototype manufacturers streamline the design process, which not only enhances creativity but also significantly reduces time to market.
The Importance of Rapid Prototyping in Modern Business
Rapid prototyping is essential for businesses across various sectors, including consumer electronics, automotive, aerospace, and medical devices. The ability to swiftly create functional prototypes allows companies to test their designs and gather feedback early in the development process. This leads to improved products and greater customer satisfaction.
Key Benefits of Rapid Prototyping
- Accelerated Design Process: Rapid prototyping speeds up the prototyping phase, allowing companies to iterate on designs more quickly than ever before.
- Cost Efficiency: By identifying design flaws early, businesses can avoid costly changes later in the production cycle.
- Enhanced Collaboration: Prototypes facilitate better communication between design teams, stakeholders, and clients, ensuring everyone is aligned on the project goals.
- Improved Market Readiness: Fast-track product development enables companies to respond quickly to market demands and trends, ensuring they stay competitive.
What to Look for in Plastic Rapid Prototypes Manufacturers
Choosing the right plastic rapid prototypes manufacturer is pivotal for your business success. Here are critical factors to consider:
1. Technological Capabilities
The best manufacturers invest in state-of-the-art technologies, including 3D printing, computer-aided design (CAD), and various molding techniques. Ensure that the company you choose has experience across multiple technologies to offer you the best possible solutions.
2. Experienced Design Team
A knowledgeable design team makes a significant difference in the quality of prototypes. Look for manufacturers that employ skilled engineers and designers who can contribute valuable insights and improvements to your prototypes.
3. Quality Control Measures
Quality assurance is vital in the prototyping process. Ensure that the manufacturer adheres to strict quality control protocols and has the certifications to back it up. This guarantees that the prototypes produced meet industry standards.
4. Quick Turnaround Times
In a competitive market, the ability to produce prototypes quickly can provide a crucial advantage. Discuss lead times with potential manufacturers to determine their efficiency in meeting your deadlines.
5. Customer Support
Choose a manufacturer that values customer relationships. Excellent customer support can help you navigate any challenges that may arise during the prototyping phase.
The Process of Working with Plastic Rapid Prototypes Manufacturers
The journey from concept to prototype involves several critical stages, each designed to refine the product and enhance its market viability. Here is a breakdown of commonly followed steps:
1. Initial Consultation
The process begins with a thorough consultation where you discuss your product requirements, goals, and specific needs with the manufacturer. This stage is crucial for setting expectations and understanding the project scope.
2. Design Development
Once the specifications are agreed upon, the manufacturer’s design team sketches initial concepts and develops 3D models. This step often involves creating digital renders that provide a clear vision of the final product.
3. Prototype Fabrication
After the designs are finalized, the actual prototyping begins. Using advanced technologies, manufacturers create prototypes that can either be functional or visual representations, depending on your needs.
4. Testing and Feedback
With the prototypes in hand, businesses can conduct tests to evaluate their functionality, usability, and overall performance. Collecting feedback from stakeholders and potential users can be invaluable for making necessary adjustments.
5. Iteration
Based on the feedback, revisions are made, and a new prototype may be developed to further refine the design. This process can cycle several times until the final product meets all requirements and expectations.
6. Final Approval and Production
Once the prototype is approved, the manufacturer can move towards mass production, ensuring that the transition from prototype to final product is seamless.
The Future of Plastic Rapid Prototyping
As technology continues to evolve, the landscape of plastic rapid prototyping is poised for even more dramatic changes. Several trends are emerging that could further revolutionize how manufacturers create prototypes:
1. Advanced Materials
The introduction of new materials, including flexible plastics and high-strength composites, is enhancing the capabilities of prototypes. This allows businesses to test more complex designs that better mimic the final product.
2. Automation and AI Integration
Incorporating automation and artificial intelligence into the prototyping process could dramatically speed up production times and reduce human error, leading to faster iterations and improved outcomes.
3. Sustainable Practices
With growing awareness of environmental issues, manufacturers are increasingly focusing on sustainable practices. This includes utilizing recyclable materials and environmentally friendly production processes to meet consumer demands for greener products.
4. Cloud-Based Design Collaboration
As remote work becomes more prevalent, manufacturers are leveraging cloud-based platforms to facilitate design collaboration. This makes it easier for distributed teams to work together on prototypes in real-time, regardless of their location.
5. Enhanced Customization
Future advancements may provide even greater customization options, allowing businesses to tailor every aspect of their prototypes to meet unique specifications and preferences, thus enhancing consumer satisfaction.
Conclusion
In conclusion, plastic rapid prototypes manufacturers are essential partners in the modern product development landscape. Their expertise, combined with cutting-edge technologies, empowers businesses to innovate faster and more effectively than ever before. As we continue to navigate a world increasingly reliant on rapid development and customization, aligning with the right manufacturer can make all the difference in bringing your vision to life. Embrace the future of product development with confidence, knowing that the right plastic rapid prototypes manufacturer can guide you every step of the way.