The Comprehensive Guide to Concrete Batching Plant
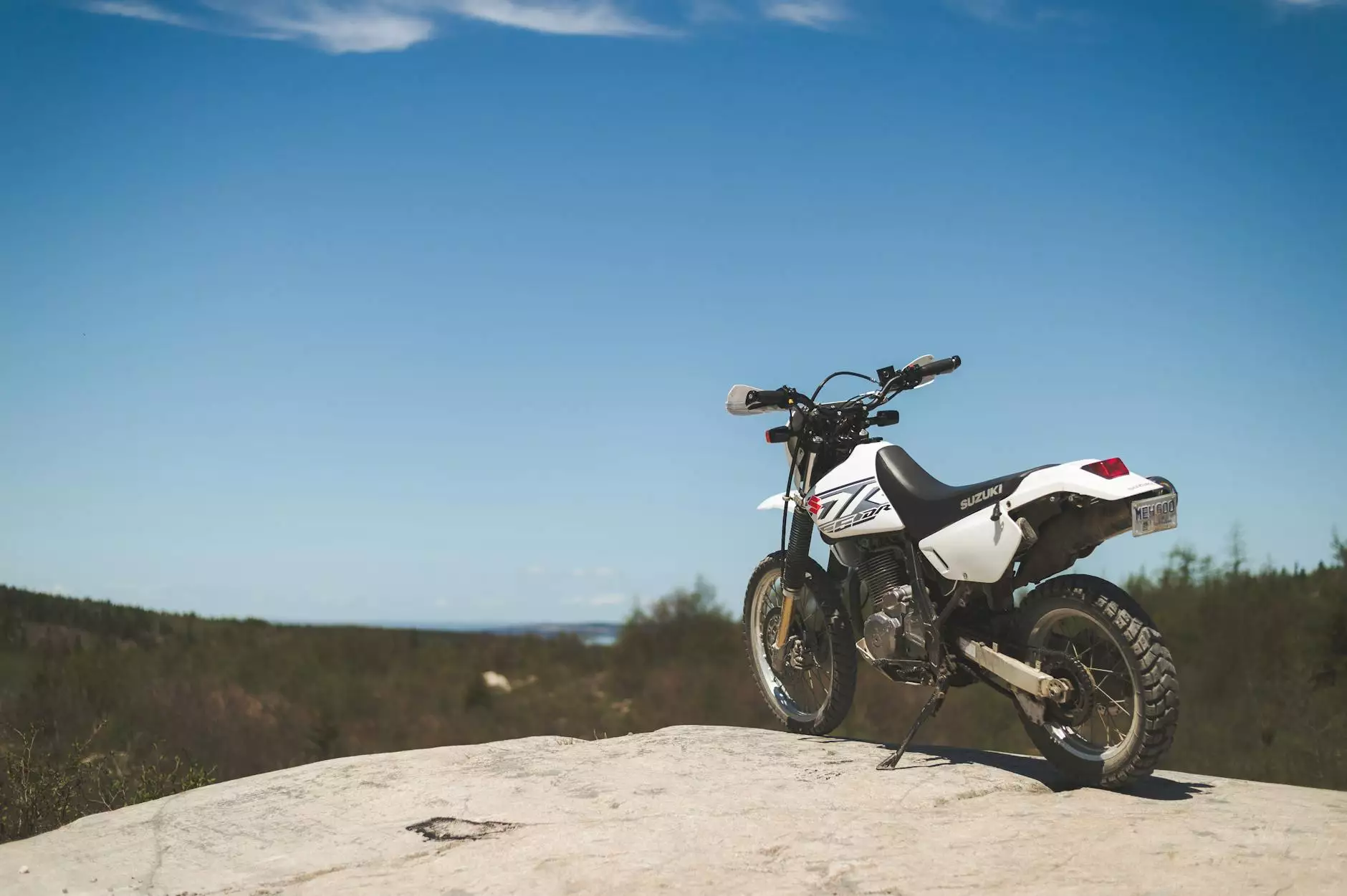
The concrete batching plant is a pivotal component in the modern construction industry. It plays an essential role in the manufacturing of concrete, enabling the creation of various concrete mixes tailored to specific project requirements. In this article, we will delve into the intricacies of concrete batching plants, their functionality, advantages, and their impact on enhancing construction efficiency and quality.
What is a Concrete Batching Plant?
A concrete batching plant is a facility that combines various ingredients to form concrete. The ingredients generally include sand, gravel, water, cement, and any other desired additives. Depending on the type of concrete required, the combination of these materials can vary. The batching plant is equipped with machinery that facilitates the precise weighing, mixing, and transporting of concrete, ensuring that the final product meets the required specifications.
Types of Concrete Batching Plants
There are primarily two types of concrete batching plants:
- Static Batching Plant: Typically used for larger projects, this type of batching plant is fixed in a single location. It is more efficient for mass production and can handle larger volumes of concrete.
- Mobile Batching Plant: Designed for flexibility and mobility, this plant can be easily transported to various construction sites. It is ideal for smaller projects and locations with limited space.
Components of a Concrete Batching Plant
Understanding the components of a concrete batching plant helps in appreciating its functionality. Key components include:
- Aggregate Bins: These hold the various aggregate materials such as sand, gravel, and crushed stone used in concrete.
- Weighing Systems: Accurate weighing systems ensure that the correct proportions of materials are used, crucial for maintaining the quality of concrete.
- Mixer: The mixer blends all the ingredients uniformly to produce high-quality concrete.
- Cement Silos: These silos store the cement used in the concrete mix and ensure a controlled supply.
- Control System: An automated control system manages the operations of the batching plant, allowing for precision and efficiency.
How Concrete Batching Plants Operate
The operation of a concrete batching plant can be summarized in a few critical steps:
- Feeding: Raw materials are loaded into the respective bins by loader or other means.
- Weighing: The materials are weighed according to the desired concrete mix design.
- Mixing: Weighed materials are pushed into the mixer for thorough mixing.
- Discharging: The mixed concrete is discharged and can be transported directly to the construction site.
Benefits of Using Concrete Batching Plants
Investing in a concrete batching plant provides numerous benefits for construction companies:
- Improved Quality Control: Automated batching ensures consistent quality across batches.
- Efficiency: A well-managed batching plant accelerates the production process, reducing delays on construction sites.
- Cost-Effective: By optimizing the use of materials and minimizing waste, batching plants can significantly reduce project costs.
- Customization: Different projects require different concrete compositions, and batching plants allow for this versatility.
Applications of Concrete Batching Plants
Concrete batching plants are utilized in a wide range of construction applications, including:
- Residential Construction: Essential for producing concrete for foundations, driveways, and sidewalks.
- Commercial Projects: Used for creating commercial buildings, shopping centers, and offices.
- Infrastructure Development: Critical in constructing bridges, roads, tunnels, and other infrastructure projects.
- Precast Concrete Production: Batching plants are vital for producing precast elements that are assembled on-site.
Challenges and Solutions in Operating a Concrete Batching Plant
Despite their advantages, concrete batching plants can face several challenges:
- Maintenance: Regular maintenance is crucial to avoid downtime. Implementing a robust maintenance schedule can address this issue.
- Environmental Concerns: Dust and water usage can be regulated by adopting eco-friendly practices and technologies.
- Quality Assurance: Continuous monitoring of the production process ensures that the quality of concrete remains high.
Future Trends in Concrete Batching Technology
The concrete industry is continuously evolving, and several trends are shaping the future of concrete batching technology:
- Automation: Increasing automation in batching plants promises improved efficiency and reduced human error.
- Green Practices: Eco-friendly concrete production practices are gaining traction, aiming to reduce the carbon footprint of construction.
- Smart Technology: Integration of IoT and smart technologies facilitates real-time data monitoring and better decision-making.
Conclusion
In conclusion, the concrete batching plant stands out as an indispensable asset in the construction industry. It not only enhances the efficiency of concrete production but also ensures that the quality of concrete meets stringent industry standards. As technology advances, we can anticipate further improvements that will make concrete batching even more efficient and sustainable. Companies like polygonmach.com are leading the way in providing state-of-the-art batching plants that cater to the evolving needs of the construction sector. Investing in such innovative solutions is key to staying competitive in a rapidly changing market.
Whether you are involved in residential projects or large-scale infrastructure developments, understanding and utilizing concrete batching plants effectively can lead to remarkable improvements in productivity and cost management.