Unleashing the Power of Pressure Die Casting Products for Your Business
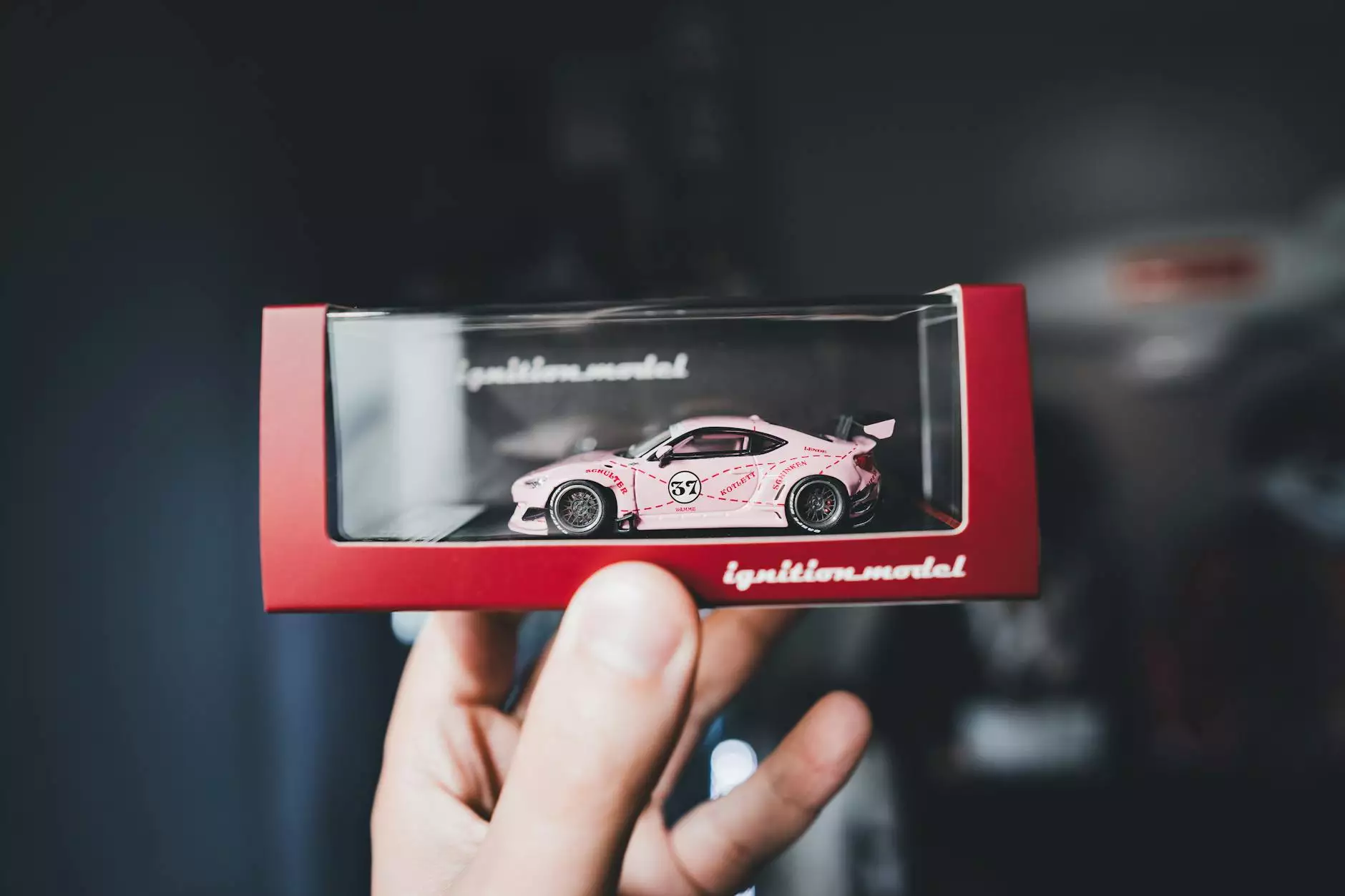
The metal fabrication industry is constantly evolving, and one of the most efficient and versatile methods utilized in this sector is pressure die casting. This advanced manufacturing process allows the creation of high-quality, intricate metal components with exceptional precision. In this comprehensive article, we will delve deep into the pressure die casting products, exploring their benefits, applications, and how they can significantly enhance your business operations.
What is Pressure Die Casting?
Pressure die casting is a metal casting process that involves forcing molten metal under high pressure into a mold cavity. This method is primarily used for non-ferrous metals, such as aluminum and zinc, and it has become favored across various industries due to its speed and efficiency. The result is durable products that require minimal processing finishing, making them ideal for numerous applications.
The Advantages of Pressure Die Casting Products
There are several significant benefits associated with utilizing pressure die casting products. Some of these include:
- High Precision and Detail: The pressure die casting process enables the production of parts that meet tight tolerances and intricate designs, resulting in high-quality end products.
- Rapid Production: The ability to produce large quantities in a relatively short period is a vital advantage. This efficiency helps businesses meet rising demand without sacrificing quality.
- Material Utilization: The process minimizes waste, allowing for maximum material utilization. This eco-friendly aspect suits today’s sustainability trends.
- Excellent Surface Finish: Products made via pressure die casting often require little to no additional finishing work due to their smooth surface, thus reducing labor costs and production time.
- Versatility: Suitable for various industries, including automotive, aerospace, and electronics, pressure die casting is adaptable to different applications and requirements.
Applications of Pressure Die Casting
Pressure die casting products are utilized in a myriad of applications across diverse sectors:
1. Automotive Industry
The automotive sector heavily relies on pressure die casting for manufacturing parts such as engine blocks, transmission housings, and various structural components. The durability and lightweight nature of aluminum die-cast parts significantly contribute to enhanced vehicle performance and fuel efficiency.
2. Aerospace Components
In the aerospace industry, the demand for high-performance materials is crucial. Pressure die casting allows for the creation of complex designs with precise tolerances, making it ideal for components like brackets, housings, and connectors that require robustness and lightweight characteristics.
3. Electronics Manufacturing
As electronics become increasingly miniaturized, manufacturers must produce intricate parts that can withstand rigorous use. Pressure die casting provides the required reliability and efficiency, offering products like heat sinks, enclosures, and connectors essential for various electronic devices.
4. Industrial Equipment and Machinery
In the manufacturing of industrial equipment and machinery, pressure die casting is used to produce components such as housings for pumps and motors, ensuring optimal performance and durability necessary for heavy-duty applications.
Understanding the Pressure Die Casting Process
The pressure die casting process involves several key stages:
Step 1: Preparing the Mold
The first step involves designing and preparing a durable mold, typically made of high-strength steel, which can withstand the high pressures and temperatures of molten metal.
Step 2: Melting the Metal
The metal, often aluminum or zinc, is heated until it reaches a molten state. This is carefully monitored to maintain the correct temperature for proper flow and filling of the mold.
Step 3: Injection of Molten Metal
The molten metal is injected into the prepared mold cavity under high pressure, ensuring the metal fills every intricate detail of the mold. This pressure is maintained until the metal solidifies.
Step 4: Cooling and Ejection
Once the molten metal cools and solidifies, the mold opens to eject the newly formed part. This process can occur in a matter of seconds, showcasing the efficiency of pressure die casting.
Step 5: Finishing Processes
While pressure die casting produces components with excellent surface finishes, additional processes such as machining or surface treatment can further enhance the product's characteristics, depending on the specifications required.
Choosing the Right Die Casting Manufacturer
When it comes to selecting a manufacturer for your pressure die casting products, consider the following factors:
- Experience and Expertise: Look for a manufacturer with a proven track record in the industry, demonstrating expertise in producing high-quality die-cast components.
- Technological Capabilities: Advanced machinery and technology can significantly impact the quality and efficiency of the die casting process. Ensure the manufacturer invests in the latest technologies.
- Customization Options: Your business may have specific requirements. Choose a manufacturer that offers customization options tailored to your needs.
- Quality Assurance: A reputable manufacturer will have quality control measures in place, ensuring that all products meet the required standards.
The Future of Pressure Die Casting Products
The pressure die casting industry is on an upward trajectory, with continuous advancements bringing forth newer, more sustainable technologies. Innovations such as improved material compositions and the integration of automation and intelligent systems are poised to revolutionize the way products are manufactured. As industries increasingly focus on reducing their carbon footprint, pressure die casting will likely play a pivotal role in sustainable manufacturing.
Conclusion
In conclusion, pressure die casting products represent a cornerstone of modern manufacturing within the metal fabrication industry. Their numerous advantages, ranging from precision to sustainability, make them preferable for various applications. By investing in high-quality pressure die casting solutions, businesses can enhance their product offerings, streamline production processes, and stand out in an increasingly competitive marketplace. For tailored solutions that meet your business needs, consider reaching out to Deepmould.net today.